What are the processing methods for titanium pipe fittings?
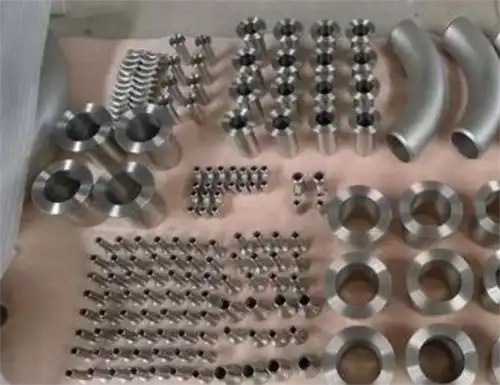
There are many processing methods for titanium pipe fittings, many of which fall into the category of mechanical processing. The most commonly used methods are stamping, forging, roller processing, rolling, bulging, stretching, bending, and combined processing. Law. Pipe fitting processing is an organic combination of machining and metal pressure processing.
Here are some examples:
Forging method: Use a swaging machine to stretch the end or part of the pipe to reduce the outer diameter. Commonly used swaging machines include rotary, connecting rod, and roller types.
Stamping method: Use a tapered core on a punch to expand the pipe end to the required size and shape.
Roller method: Place a core inside the tube and push the outer circumference with a roller for round-edge processing.
Rolling method: generally does not require a mandrel and is suitable for the inner round edge of thick-walled pipes.
Bending forming method: There are three commonly used methods, one method is called the stretching method, the other method is called the stamping method, and the third method is the more familiar roller method, which has 3-4 rollers, two fixed rollers, and one adjusting roller. Roller, adjust the fixed roller distance, and the finished pipe fitting will be curved. This method is widely used. If spiral tubes are produced, the curvature can be increased.
Bulging method: one is to place rubber inside the tube, and use a punch to compress it above to make the tube bulge into shape; the other method is hydraulic bulging, in which liquid is filled into the middle of the tube, and the liquid pressure bulges the tube into the required shape. Most of our commonly used corrugated pipes are produced using this method.